The UC Davis Facility for Interconnect Technologies (UCD-FIT) has been developing methods for removing the negative aspects of gold-studs, in order to make them a viable option for a wide variety of prototyping needs. This paper explores double gold-stud bonding as a method of reducing the bonding stresses, and 0.5 mil gold wire studs as a technique for bonding smaller devices.
Development for this project began during our work with the PSEC waveform sampling ASIC for the Large Area Picosecond Photo-Detector (LAPPD) collaboration. The periphery of the PSEC chip contains 118 square pads, each 62 μm on a side, with a pitch of 130 μm. As shown in Figure 1, gold-studs formed using 1 mil wire are too large and would cause shorts during thermocompression.
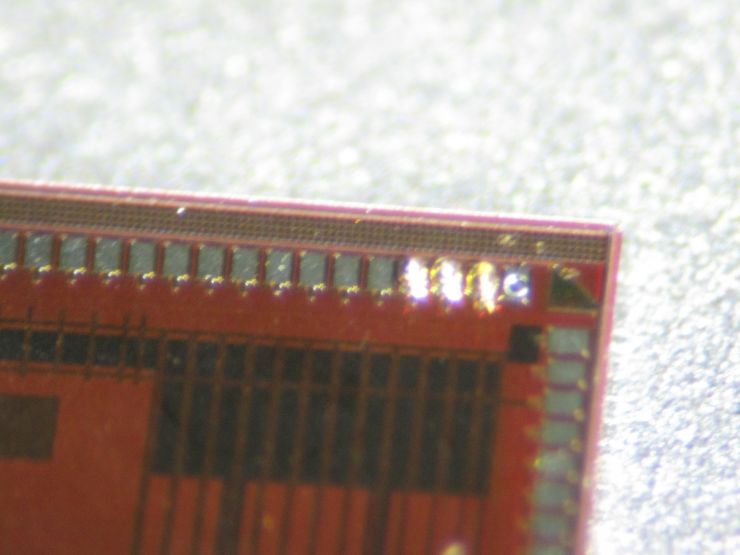
In response to this problem we began using 0.5 mil (12.7 μm) gold wire to form smaller gold studs. The procedure with 0.5 mil wire uses the same Westbond Ball bonder as the 1 mil wire, albeit with a smaller capillary. The thinner wire also necessitates different settings for the ultrasonic power and studding force. We have determined that using an ultrasonic energy of 400 for 45 ms yields a greater fraction of properly formed studs, and with greater adhesion strength to the substrate. Using these settings, we have been able to achieve stud collar sizes of 87 +/- 4 μm, significantly smaller than 104 +/- 6 μm from the 1 mil wire.
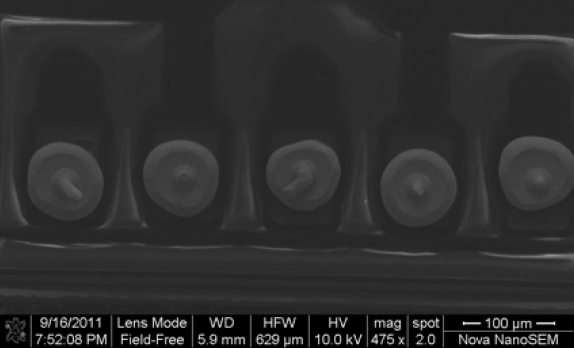
FIgure 2 has an example of such smaller gold-studs, showing a scanning electron microscope (SEM) picture of the gold studs. We have also performed a successful thermo-compression bond of a prototype PSEC using the pressure and temperature typically used for 1 mil wire studs. This assembly is being tested by the LAPPD collaboration.
Despite achieving smaller gold-studs, we are aware of difficulties with the 0.5 mil wire that must be addressed. In particular, the gold wire is much more difficult to handle compared to its thicker counterpart. The wire is prone to bending and kinking while threading through the capillary, which results in far more time being spent preparing the bonder. Faults in the machine are also more likely to occur. The specific sonication properties need to be more thoroughly quantified because higher studding forces flatten the gold studs into larger diameters. Therefore, further work is required to find the lowest amount of force that still forms a strong stud-to-pad connection.